Early last year in a previous blog, we discussed Triangle®’s recent growth in employees, facility space, and production technology. Today we are highlighting those technological improvements in the production processes of our reciprocating pump components at both manufacturing facilities and relaying how these changes increased our ability to bring our quality products to our customers with a much faster turnaround.
Making a huge impact in valve component production at our Cleburne TX facility is our new robot/”employee”, Arturito. Named by CNC machinist, Luis Marquez, Arturito was given the nickname for what Luis saw as TPCI’s equivalent of R2D2. Two TPCI employees, Luis and Delson, completed 32 hours of training on the Fanuc Robot CRX-20iA/L which runs our CNC machine GT-250B. According to Luis, to compare the output between a person and the robot; a person can run one CNC machine and produce approximately 50-60 parts per day whereas Arturito can currently run up to 80 parts per day.
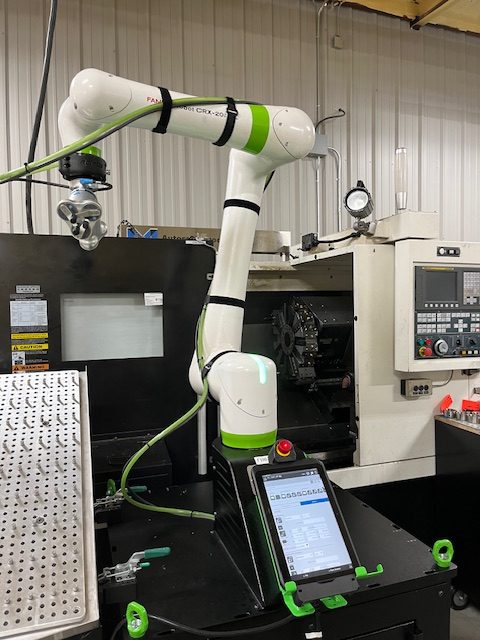
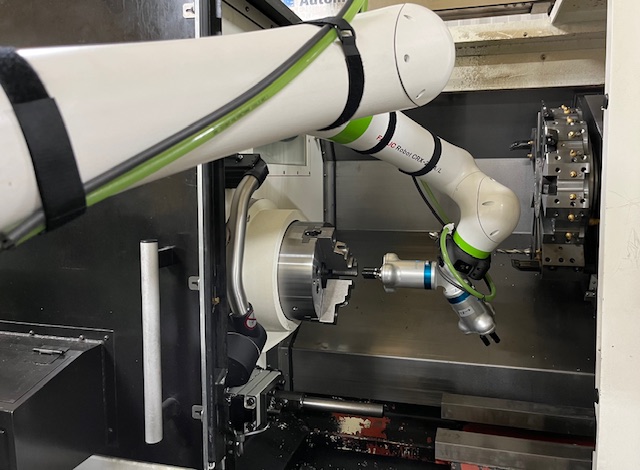
TPCI-Cleburne also acquired a new mill that made another big difference in valve component production. It has double the capacity with 25 horsepower, 50 taper (more stable) 3 axis, through spindle high pressure coolant. Our resident expert on the mill, Chris Gierhahn, describes it with the following:
- Produces more accurate parts than you can achieve with traditional methods.
- Delivers products with constant dimensions.
- Allows for production of larger parts in larger quantities.
- Runs at faster speeds which reduces manufacturing costs.
- Permits creation of complex designs
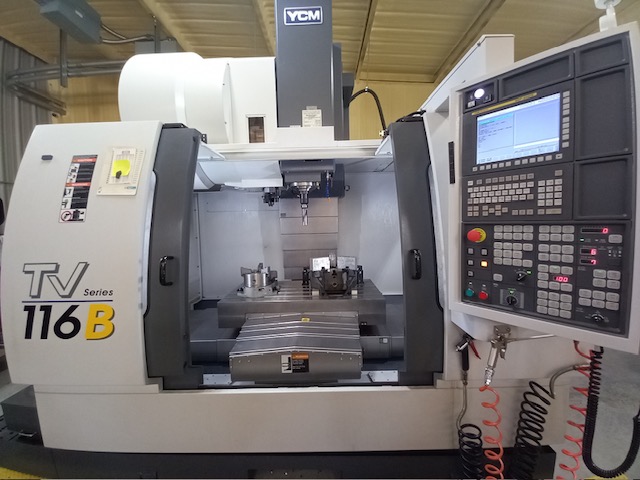
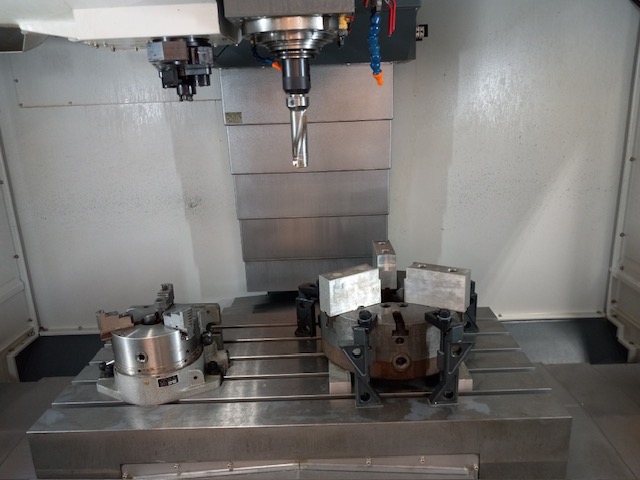
Adding the finishing touch to the valve components in Cleburne is the Geo. T. Schmidt Inc. (GTS) STYLINER® Mark4 marking machine. It has an 8” x 8” marking area and a low stress dot pin capable of marking our reciprocating pump valve components at a faster pace with ease. Required by some customers, this machine is completely programmable with software based off AutoCAD and produces professional-looking text, symbols, and logos per Jon Edson, Cleburne’s Production Manager.
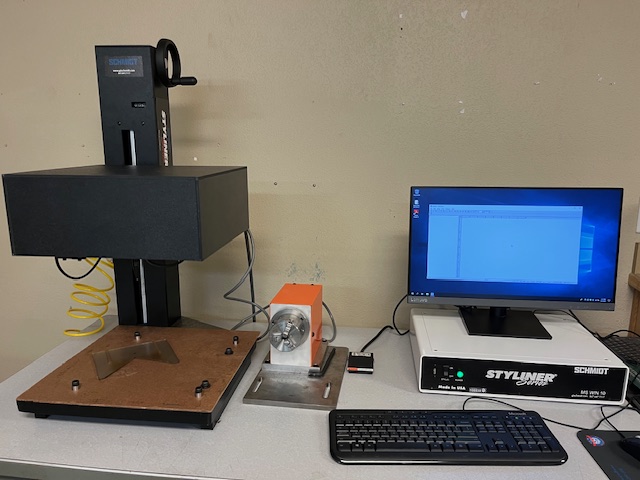
Our Oklahoma City OK plunger and packing manufacturing facility has also invested in processes to help streamline their parts productions. Mark Otwell, Operations Manager of the OKC facility, describes how they have incorporated both preventive maintenance and technology to improve their production process as follows:
- We added a galvanized Tee with a plug to all the coolant lines of the four NC Grinders and the Manual Grinder to be able to attach a spray hose to clean the machines (when needed). Instead of taking a lot of time to wipe down each machine, a quick five-minute spray gets the job done efficiently.
- In an enclosed cabinet, we’ve housed one computer that networks all our CNC machines together to keep all the programs centralized so the machinists can pull up any program and send it to whichever machine needs it. Each machinist can now send every program they need for the day to their machines at the same time eliminating the need to go back & forth after each job, which also saves quite a bit of time.
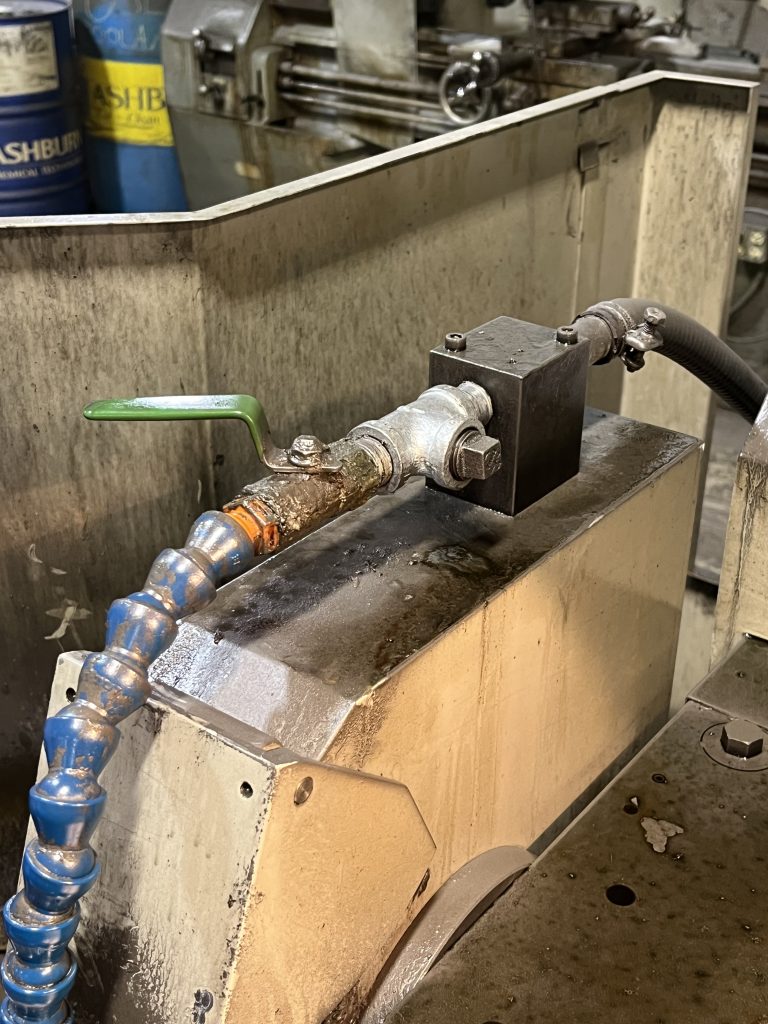
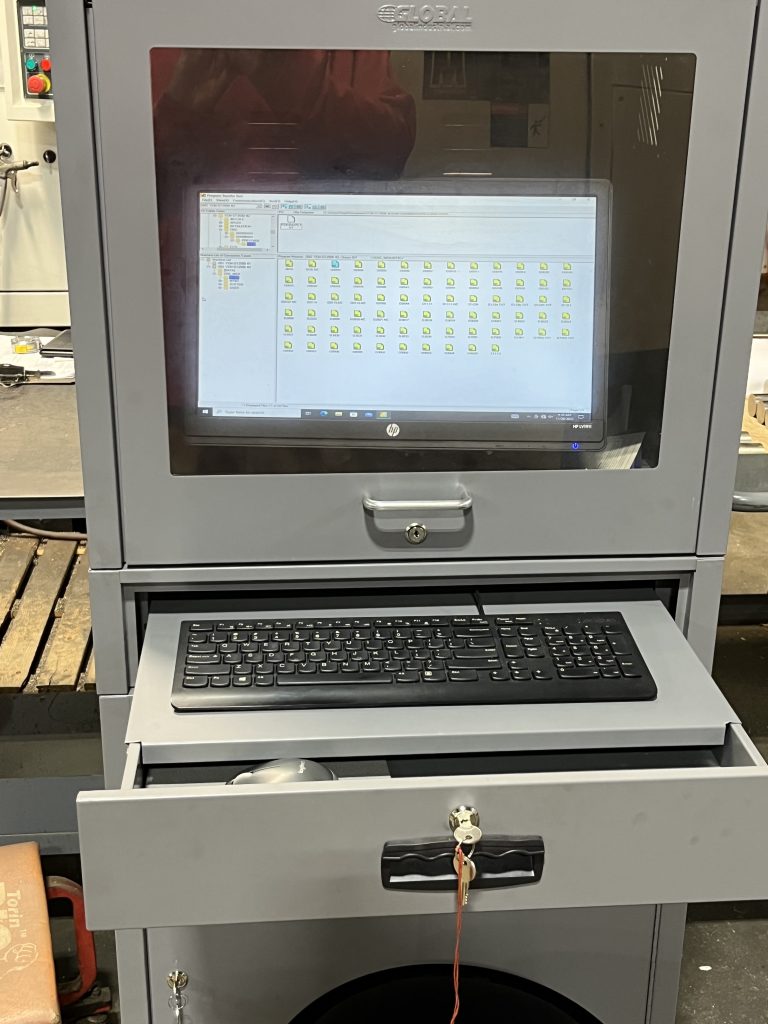
All these additions to our valve, plunger, and packing manufacturing processes have positioned TPCI as the leader in manufacturing quality reciprocating pump component products and allowed us to deliver them to our customers in a timely manner. Contact us to help your pump run smoothly and efficiently with our superior valves, plungers, packing, and stuffing box components.